Electric Plastic Molding: A Comprehensive Guide
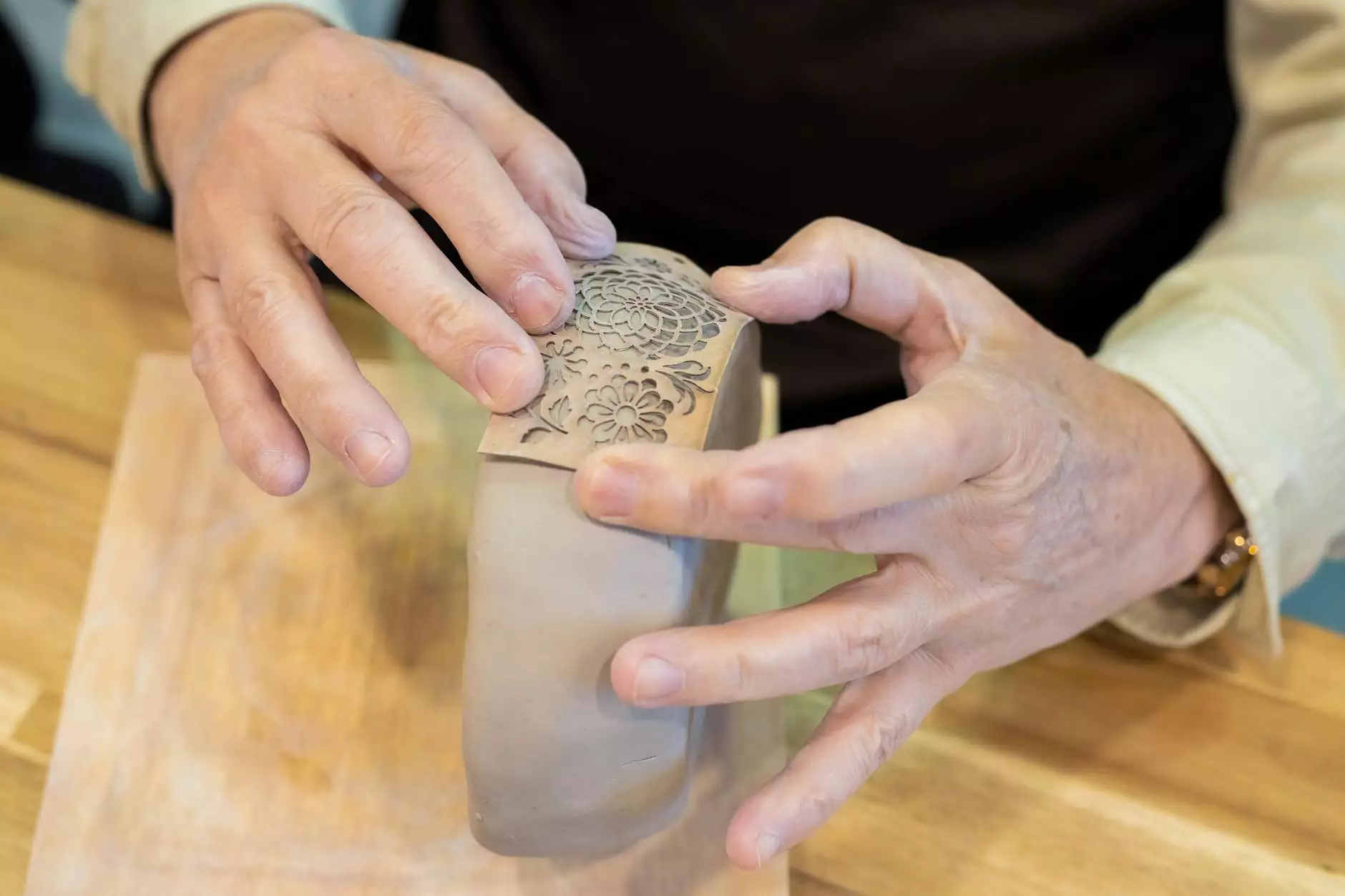
Electric Plastic Molding is revolutionizing the manufacturing landscape by providing an efficient and environmentally-friendly alternative to traditional molding techniques. This technology has become a cornerstone in numerous industries, including automotive, electronics, consumer goods, and medical devices. In this article, we will delve into the workings of electric plastic molding, its benefits, applications, and how it compares to other molding processes.
Understanding Electric Plastic Molding
Electric plastic molding is a process that uses electric power to drive the injection molding machine, as opposed to hydraulic systems utilized in traditional methods. The primary components of an electric plastic molding machine include:
- Electric Motors: These are responsible for driving the various functions of the machine, including injection, clamping, and ejection.
- Injection Unit: This unit heats and injects the plastic material into the mold.
- Molding Station: Where the plastic solidifies into the desired shape.
- Control System: Modern electric machines come equipped with programmable logic controllers (PLC) that allow for precise control of the molding process.
Advantages of Electric Plastic Molding
The shift towards electric plastic molding brings numerous advantages that make it an attractive option for manufacturers:
1. Enhanced Precision and Consistency
One of the standout features of electric plastic molding is its ability to produce intricate parts with a high degree of accuracy. The electric motors provide consistent pressure and speed, which results in:
- Uniform wall thickness
- Reduced tolerances
- Elimination of defects such as short shots or warping
2. Energy Efficiency
Electric plastic molding machines consume significantly less energy compared to hydraulic machines. This efficiency arises because electric motors only draw power as needed, thus:
- Reducing overall energy costs
- Lowering carbon footprint of the manufacturing process
3. Reduced Maintenance Costs
Hydraulic systems typically require more maintenance due to the complexity of the hydraulic fluid systems. Electric machines, on the other hand, have fewer moving parts, leading to:
- Lower maintenance requirements
- Extended machine lifespan
4. Quiet Operation
The operation of electric machines is quieter than that of hydraulic machines, contributing to a more pleasant working environment. This can also lead to:
- Improved worker morale
- Reduced noise-compliance costs
Applications of Electric Plastic Molding
The versatility of electric plastic molding allows it to be used in various industries. Here are some of its notable applications:
1. Automotive Industry
Components such as dashboards, light housings, and internal trim parts are often produced using electric plastic molding due to the precision and surface finish achievable with this method.
2. Consumer Electronics
The demand for smaller, more intricate designs in consumer electronics like smartphones, tablets, and wearable devices makes electric plastic molding a preferred choice for manufacturers.
3. Medical Devices
The medical field frequently relies on electric plastic molding to produce components such as syringes, surgical instruments, and diagnostic equipment. The precision and cleanliness of the process ensure compliance with stringent industry standards.
4. Packaging Industry
With the rise in e-commerce, the packaging industry is seeing increased use of electric molding for creating lightweight, durable packaging materials. This is crucial for protecting products while reducing shipping costs.
Comparison with Traditional Molding Methods
To fully appreciate the benefits of electric plastic molding, it is essential to compare it with traditional molding methods, such as hydraulic molding:
- Energy Consumption: Electric molding uses less energy, while hydraulic systems tend to use more due to constant pressure and flow.
- Precision: Electric systems provide better precision, making them superior for intricate designs.
- Speed: Electric machines can perform cycles more quickly due to faster clamp and injection times.
- Maintenance: Fewer components in electric machines lead to reduced wear and lower maintenance needs compared to hydraulic machines.
Future of Electric Plastic Molding
As technology advances, the future of electric plastic molding looks promising. Innovations in:
- Machine Learning: Implementing AI and machine learning can enhance process optimization and predictive maintenance.
- Advanced Materials: The development of bio-degradable and high-performance plastics will expand the applications of electric molding.
- Automation: Increased automation in electric plastic molding processes can ramp up production and reduce costs.
Conclusion
In conclusion, Electric Plastic Molding has emerged as a key technology in the modern manufacturing landscape, offering numerous advantages over traditional methods. From enhanced precision to energy efficiency and reduced maintenance costs, the benefits are substantial. As the manufacturing industry continues to evolve, embracing electric plastic molding could position businesses like those found at deepmould.net at the forefront of innovation. The applications are vast, and the future is bright for those who adopt this advanced technology.