The Power of a Plastic Injection Molder in Modern Manufacturing
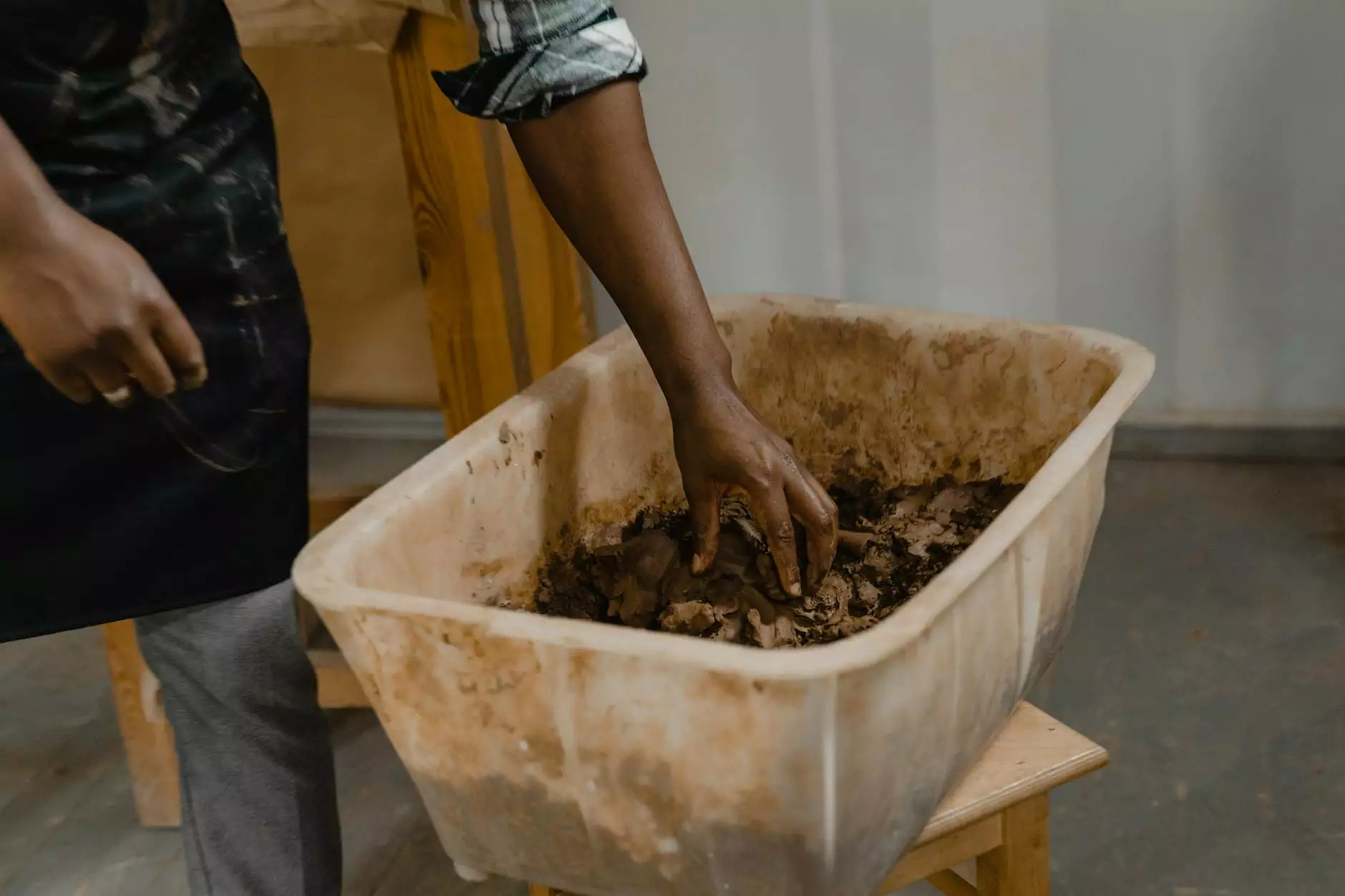
In today’s fast-paced world, businesses are constantly looking for ways to streamline operations and enhance production efficiency. One of the most revolutionary technologies contributing to this goal is the plastic injection molder. This powerful tool transforms thermoplastic materials into intricate designs, providing unparalleled versatility in manufacturing processes.
Understanding Plastic Injection Molding
Plastic injection molding is a manufacturing process that involves injecting molten plastic into a mold to create various shapes and components. This method offers numerous advantages over traditional manufacturing techniques, such as:
- High Efficiency: Rapid production cycles allow for large quantities of products to be made in a short period.
- Precision and Accuracy: Molds are crafted with precision, ensuring consistent product quality.
- Material Versatility: A wide range of thermoplastic materials can be used, accommodating various requirements.
Key Benefits of Using a Plastic Injection Molder
Investing in a plastic injection molder can have a transformative impact on your business. Here are some significant benefits:
1. Cost-Effectiveness
Although the initial costs for setting up plastic injection molding can be high, the long-term savings are substantial. After the mold is created, subsequent production runs become incredibly economical, especially with mass production.
2. Enhanced Design Flexibility
Modern injection molding technology allows designers greater freedom in creating complex shapes and intricate designs that would be difficult or impossible to achieve with other manufacturing methods.
3. Improved Product Quality
The precision of a plastic injection molder ensures that each product meets stringent quality standards. This consistency minimizes waste and reduces the need for post-production alterations.
4. Speed of Production
Injection molding can produce thousands of parts per hour. This speed meets market demands swiftly, making it easier for companies to stay competitive.
The Plastic Injection Molding Process
Understanding how a plastic injection molder operates is crucial for businesses looking to leverage this technology. The process encompasses several key steps:
1. Material Selection
Selecting the right type of plastic is essential. Factors may include durability, flexibility, and resistance to environmental factors. Common materials used include:
- Polyethylene (PE)
- Polypropylene (PP)
- Polyvinyl Chloride (PVC)
- Polystyrene (PS)
2. Mold Design
The design phase is critical; this is where a mold is crafted to create the desired final product. Advanced software programs like CAD (Computer-Aided Design) are often used to design molds that allow for maximum efficiency and detail.
3. Injection Phase
In this phase, the selected plastic material is heated until it reaches a liquid state. It’s then injected under high pressure into the pre-designed mold. Once cooled, the material solidifies as it takes the mold's shape.
4. Ejection Phase
After sufficient cooling, the mold opens, and the finished plastic part is ejected. This step is crucial as it marks the transition from raw material to finished product.
Applications of Plastic Injection Molding
The versatility of a plastic injection molder spans various industries, including:
1. Automotive Industry
Injection molded parts are widely used in the automotive sector, helping create components such as dashboards, interior panels, and even engine components, all vital for reducing weight and improving fuel efficiency.
2. Consumer Goods
From toys to kitchen utensils, the consumer goods segment greatly benefits from plastic injection molding, providing durability and aesthetic appeal.
3. Electronics
In the electronics industry, injection molding is used to produce casing for smartphones, tablets, and household appliances, ensuring that products are lightweight yet tough enough to protect sensitive components.
4. Medical Devices
Plastic injection molding is fundamental in fabricating components for medical devices, pharmaceutical packaging, and laboratory equipment, adhering to high regulatory standards.
Choosing the Right Plastic Injection Molder for Your Business
Not all plastic injection molders are created equal. When selecting a provider, consider the following factors:
1. Experience and Expertise
Select a company with a rich history in injection molding and a deep understanding of different materials and technologies.
2. Technology and Equipment
Evaluate the types of machines and technology used for injection molding. Advanced machinery typically offers better precision and efficiency.
3. Customization Capabilities
Look for companies that provide design and engineering support, ensuring that your specific needs are met through bespoke solutions.
4. Quality Control Measures
Investigate their quality assurance protocols. Reliable manufacturers perform rigorous testing to guarantee the quality of the molded parts.
The Future of Plastic Injection Molding
As technology evolves, so does the landscape of plastic injection molding. The integration of automation, AI, and sustainability practices are shaping the future of this essential manufacturing process.
1. Sustainable Practices
With growing environmental consciousness, the industry is adopting practices such as recycling and using biodegradable materials, helping to minimize the ecological impact.
2. Automation and Robotics
The introduction of automation in the injection molding process is boosting efficiency. Robots can handle parts faster and more accurately, reducing labor costs and human error.
3. 3D Printing and Injection Molding
The combination of 3D printing with injection molding is paving the way for rapid prototyping and production. This integration allows businesses to test designs quickly before committing to mass production.
Conclusion
The plastic injection molder stands as a cornerstone of modern manufacturing, offering numerous benefits that drive efficiency, quality, and innovation. Whether you are in the automotive, consumer goods, electronics, or medical sectors, leveraging this powerful manufacturing process can position your business for success. As you consider incorporating injection molding technology, remember to prioritize quality, flexibility, and sustainability to stay ahead in a competitive marketplace.
To learn more about integrating plastic injection molding into your business strategy, visit deepmould.net for further insights and expert consultations.