The Evolution and Importance of the Oil Cooler Factory in Diesel Engine Parts
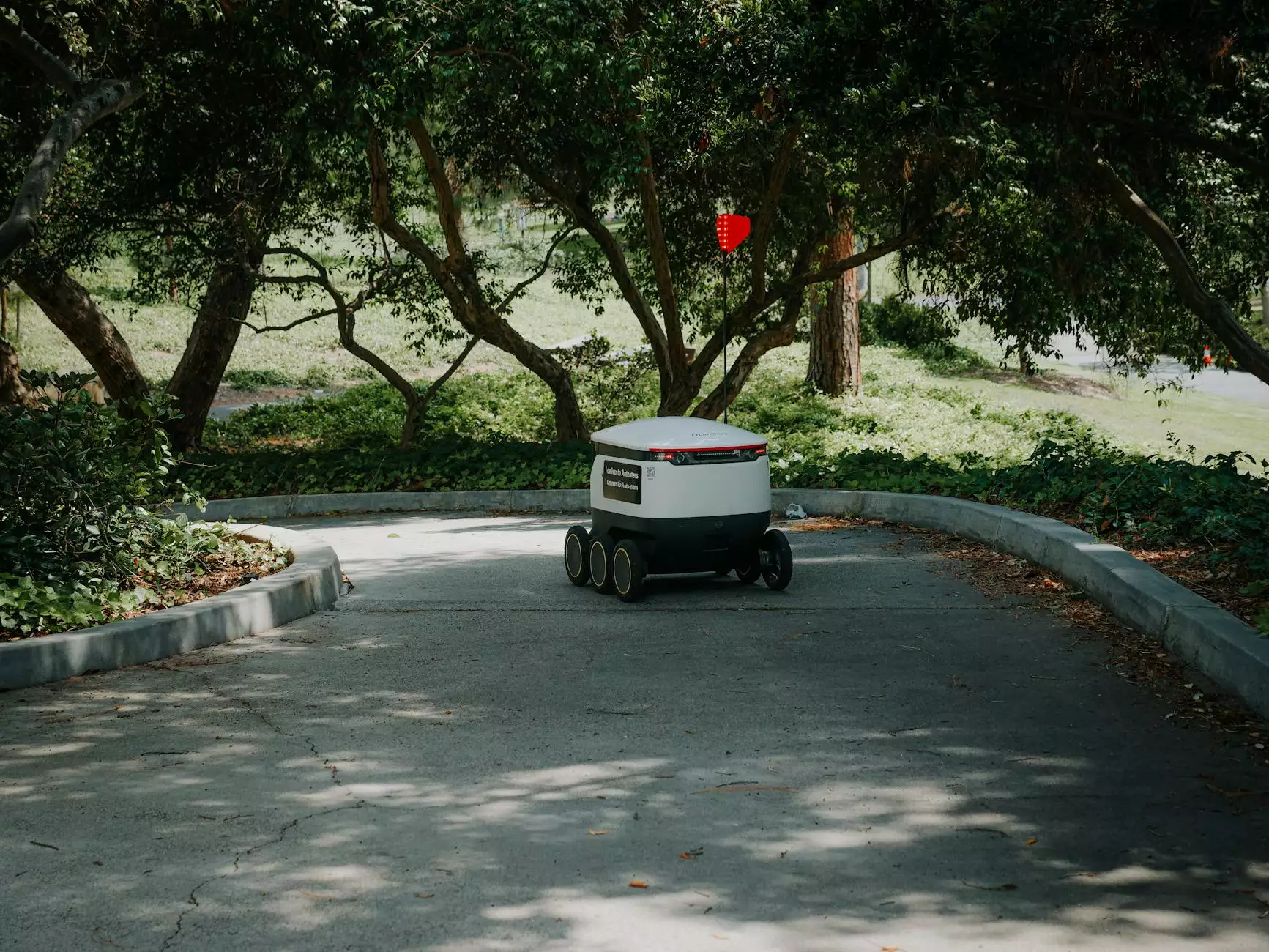
In the realm of diesel engine parts, the role of an oil cooler factory is often underappreciated yet fundamentally critical. Oil coolers are essential components that help maintain optimal operating temperatures within diesel engines, enhancing performance while preventing potentially devastating overheating scenarios. This article aims to delve into the workings of oil cooler factories, the implications for the spare parts supply industry, and the innovations that are driving this essential sector forward.
Understanding Oil Coolers and Their Purpose
Before we dissect the manufacturing processes within an oil cooler factory, it's vital to comprehend what oil coolers are and their significance in diesel engines. Simply put, oil coolers are specialized devices that regulate the temperature of engine oil running through the system. Here are some of their primary functions:
- Temperature Regulation: Maintaining the engine oil within an optimal temperature range ensures that the oil retains its lubricating properties, minimizing wear and tear on engine components.
- Performance Enhancement: Cooler oil contributes to improved engine performance and efficiency, leading to better fuel economy and reduced emissions.
- Extended Service Life: By preventing overheating, oil coolers help extend the life of diesel engines, saving costs on repair and maintenance.
The Manufacturing Process of Oil Coolers
At its core, the production of oil coolers within an oil cooler factory involves several meticulous steps. Precision and quality are paramount as any defects in construction can lead to significant engine failures. Below is an outline of the primary stages involved in manufacturing oil coolers:
1. Design and Engineering
The journey begins with a detailed design phase where engineers use advanced software to create models of the oil coolers. Factors considered during this phase include:
- Material Selection: Metal types, such as aluminum or copper, are evaluated for their thermal conductivity and durability.
- Flow Dynamics: Engineers analyze fluid dynamics to ensure optimal oil flow and cooling efficiency.
- Size and Configuration: The physical dimensions must match the specifications required by various diesel engine models.
2. Material Procurement
Once designs are finalized, the oil cooler factory sources high-quality materials. This may involve:
- Establishing relationships with reputable suppliers to procure metals and other necessary components.
- Quality inspections of incoming materials to ensure they meet stringent standards.
3. Fabrication and Assembly
This stage entails the actual creation of the oil cooler. The fabrication process includes:
- Cutting and Shaping: Materials are cut to precise shapes using laser cutting technology or CNC machining.
- Welding and Brazing: Components are then welded or brazed together to form the complete unit, emphasizing robust joining techniques to withstand high pressures.
4. Quality Control Testing
After assembly, each oil cooler undergoes rigorous testing to ensure reliability. Tests include:
- Pressure Testing: Ensures that the cooler can handle the necessary pressure without leaks.
- Performance Testing: Verifies the cooling efficiency under simulated operational conditions.
Innovative Technologies in Oil Cooler Factories
To stay competitive, oil cooler factories are increasingly adopting CNC (Computer Numerical Control) machining, automation, and 3D printing technologies. These innovations help in enhancing precision and reducing waste, which contribute positively to the environment while lowering production costs. Here are some state-of-the-art technologies utilized in the manufacturing of oil coolers:
1. Computer-Aided Design (CAD)
CAD systems enable better visual representation of designs. Engineers can simulate how the oil cooler will function and make necessary adjustments before moving to production.
2. 3D Printing
3D printing technology is increasingly utilized for creating prototypes. This not only speeds up the design process but also allows for extreme customization tailored to specific engine specifications.
3. Automation and Robotics
Using robotics for assembly can enhance precision and speed. Automated systems reduce the human error factor during repetitive tasks such as welding, thus increasing the overall quality of the finished product.
Market Trends and Future Prospects for Oil Cooler Factories
The demand for oil coolers is set to rise due to the increasing popularity of diesel engines in various sectors including transportation, agriculture, and machinery. As the world becomes more environmentally conscious, the diesel engine industry is innovating to meet new emissions standards, thereby creating new requirements for effective oil cooling solutions. Here are some trends driving the industry:
- Increased Efficiency Standards: New regulations are prompting manufacturers of diesel engines to focus on cooling solutions that maximize efficiency and minimize waste.
- Growth in Heavy-Duty Vehicles: The need for robust oil coolers is increasing as heavy-duty vehicles become more common in logistics and public transportation.
- Technological Integration: Advanced technologies in manufacturing processes are making oil cooler production faster and more cost-effective.
The Role of Spare Parts Suppliers
In conjunction with oil cooler factories, spare parts suppliers play a critical role in ensuring that quality replacements are available in the market. They act as the bridge between manufacturers and customers, providing the necessary components that support ongoing engine performance and reliability. Key aspects of this relationship include:
- Distribution Networks: Suppliers must maintain an extensive distribution network to get parts to customers quickly and efficiently.
- Customer Support: Knowledgeable staff are essential in assisting customers in selecting the right parts for their specific needs.
- Inventory Management: Effective inventory strategies ensure that popular parts are always in stock, reducing down-time for customers.
Conclusion: The Essence of Oil Cooler Factories in the Diesel Engine Market
As the demand for higher efficiency and performance in diesel engines continues to grow, the role of the oil cooler factory becomes increasingly pivotal. With innovations in manufacturing processes and materials, these factories not only contribute to the longevity of engines but also support a greener future through enhanced efficiency and reduced emissions. The synergy between manufacturing and spare parts supply is enhancing the overall quality of diesel engine components available in the market today.
The commitment to innovation, quality, and sustainability will undoubtedly shape the future landscape of oil cooler manufacturing and the wider diesel engine parts industry. As such, companies that invest in evolving practices and technologies stand to gain the most, ensuring their place as leaders in the field.